Amidst the rapidly evolving landscape of the box forming machinery sector, the demand for more efficient, sustainable, and robust machinery is escalating. Delta’s innovative automation solutions have played a pivotal role in enhancing the production capabilities of Tecnobox, a box forming machinery company in Spain. This transformation has not only fortified Tecnobox’s position in a competitive market, but it has also set new standards in the industry for technological advancement and environmental responsibility.
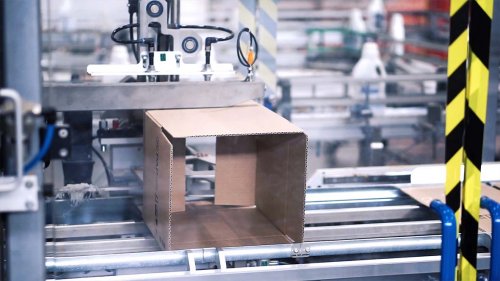
Urgent Need for a Reliable, Efficient Solution
Nestled in Levante, a bountiful food-producing region, Tecnobox is renowned for its dedication to quality, innovation, and sustainability. With around 40 employees, this medium-sized company has carved a niche in manufacturing robust, low-maintenance cardboard box assembly machinery.
Its products are distinguished by the use of standard components to speed up production and a commitment to replacing metal and plastic containers with biodegradable alternatives.
However, the post-pandemic landscape posed unprecedented challenges for the company. A critical component crisis threatened the continuity of Tecnobox’s production, putting its market leadership at risk. This crisis coincided with a period when Delta was seeking to establish a stronger presence in the market.
Tecnobox’s need was clear. It required a system that mirrored its current architecture’s reliability, while offering enhanced efficiency. The solution had to be complete and incorporate EtherCAT communication while aligning with its ethos of innovation and sustainability. With its AX3 PLC, MS300, ASDA-B3, DOP100, and LITE Power Supply. Delta emerged as the candidate most suited to meeting Tecnobox’s requirements, not just for the completeness of its offering, but also its ability to deliver it promptly.
Operating two distinct machines within the system, Tecnobox required specialized control architectures tailored to each machine’s unique tasks and performance metrics. The first machine, TB-Pack, utilizes a servo system with the MS300 drive, achieving a production speed of 3000 pieces per hour. Along with the servo system and MS300 drive, it is also equipped with an HMI, PLC, and I/O, making this machine optimally forms boxes of specific types.
The second machine, TBQ-Pack, shares a similar configuration with TB-Pack but substitutes the MS300 with another servo system, allowing it to operate at a faster pace of up to 10000 pieces per hour. These variations in control architecture stem from the distinct production requirements and speed capabilities of each machine.
A Synergy of Expertise and Innovation
The journey began with Delta’s proactive approach. Collaborating closely with its regional partner, INDA LEVANTE, Delta offered its comprehensive automation solutions to Tecnobox. This collaboration was not just about providing hardware; it involved an intricate process of understanding Tecnobox’s needs and tailoring its hardware and software solutions according to Tecnobox’s unique requirements.
Delta’s Project Managers and Field Application Engineers spearheaded the initiative, conducting extensive technical training sessions for Tecnobox and INDA LEVANTE. Within five months, a prototype machine was manufactured which integrated Delta’s advanced automation systems. As with all implementations, in the early stages there were challenges to overcome, but they served to prove Delta’s confidence in problem-solving and commitment to complete customer satisfaction.
Enhanced Performance and Cost-Efficiency
Following the implementation, the results were remarkable. Tecnobox not only overcame the production hurdles, but it did so with a solution that saved approximately 25% in electronic materials costs. Furthermore, the stability and efficiency of Delta’s solutions were not just in line with Tecnobox’s expectations, but also reinforced its market position during a critical period.
This collaboration between Delta, Tecnobox, and INDA LEVANTE transcends a mere business transaction; it exemplifies a synergy where challenges are converted into opportunities. The success story is best encapsulated in the words of Edwin Gomez Rodriguez, Field Application Engineer, Industrial Automation Business Group at Delta EMEA: “This project with Tecnobox not only demonstrates our capabilities in delivering efficient, cost-effective automation solutions but also reinforces Delta’s commitment to customer satisfaction and innovation. We’re proud to have played a key role in supporting Tecnobox through a challenging period, and this collaboration signifies a major step in our journey towards becoming a recognised name in the automation industry.”
Delta’s unwavering commitment to innovative problem-solving and customer satisfaction, coupled with Tecnobox’s strategic market insights and operational excellence, have created a formidable partnership that stands out as a beacon in the manufacturing and automation industry. The resilience and innovation serve as a compelling model for others navigating the complex landscapes of modern industry.
DELTA ELECTRONICS NETHERLANDS BV
Zandsteen 15
2132 MZ Hoofddorp
The Netherlands
Wu Judy
Phone : +31 (0)20 655 09 06 / 31(0) 611-581-859
jwu@deltaww.com